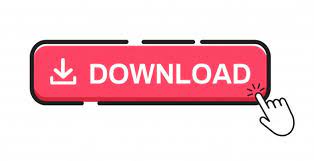
These values don’t matter, since we’re going to remove the movement paths at post-process time.You can also set up ‘tabs’ here, if desired.When selecting contours, note that a red arrow is displayed illustrating the cut direction. It seems that these must be selected individually, which is a pain in the neck for a complex project. Feed settings: don’t matter in our case.Kerf width: more on this later choose.cutting mode: ‘Through – auto’ (I’m not sure what this does but it sounds logical and worked for me).Click OK to finish the setup, then click ‘WATERJET’ to create a new contour operation, and set values on each tab as follows:.This works the same as for milling operations. I like to set WCS to ‘model orientation’, ‘stock box point’, and then choose the lower-left corner of my stock box as illustrated here.You could also enter your actual stock size if desired, but this merely serves as a visual reference perhaps as a double-check of your part layout. On the ‘Stock’ tab, I prefer to use ‘relative size box’ with all offsets set to zero.On the ‘Setup/Operation Type’ tab, choose ‘Water/laser/plasma’.Select ‘New Setup’ and set values as follows:.Enter the CAM workspace (the big gray menu on the left).Then, with the cut layout component visible and other components hidden, (…Another obvious application for a custom script or add-in.) The CAM support does nothing to help with this step. You’ll probably still want to create the ‘cut layout’ component as described above. Please leave a comment if you figure out where it is.Īlternatively, you could also follow these steps, which put the post processor in the cloud so you can use it from multiple machines. I’m sure there’s an equivalent on Windows. On a Mac, you simply copy it to this directory:
#SLICER FOR FUSION 360 SAYS MATERIAL IS TOO SMALL INSTALL#
Install this post processor in your Fusion environment.Save the ‘dxf.cps’ file to your machine.Then scroll down to ‘AutoCAD DXF’ and click ‘download’.In the ‘type’ dropdown, choose ‘Water / Laser / Plasma’.Next, install the DXF ‘Post Process.’ This allows saving the tool path as a DXF file. Then select ‘Preview’ and turn on ‘CAM – Water/Laser/Plasma cutter support.’ These steps may become unnecessary when the feature passes out of the preview phase.įirst turn the feature on: select ‘Preferences’ under your user name in the upper right corner. The new CAM support promises to address these shortcomings in a way that works more like the CAM workflow for milling or ‘CNC routing.’ To use it there are a few preliminary steps that must be done just once. Please post if you have an alternate technique! It’s an obvious application for a script or add-in, and I suspect something’s available but haven’t looked for it yet. If you didn’t get the kerf adjustment right the first time, or if your part dimensions or layout change, you must repeat these laborious steps. Obviously, this is a major pain in the neck to maintain. I like to draw a small circle where I want the tab use the ‘trim’ tool to delete the portion within the circle then delete the circle. If you want ‘tabs’ to keep the pieces in the material sheet, they must be manually created: delete a small portion of the path at each desired location.(It’s probably smart to make a copy of your cut layout sketch first). Select the original profile and delete it.Apply the ‘offset’ tool, creating a new profile just outside the original.Edit the cut-layout sketch Select each profile in turn and:.We can adjust for kerf by doing some additional work right before exporting: Sometimes this doesn’t matter, but for parts that must precisely fit together (like the ubiquitous finger-jointed boxes) it can be an annoying problem. The principal shortcoming of this approach is that the projected contours aren’t adjusted for the kerf of the laser cutter. Create a new sketch and project all parts on the cut layout to the sketch plane.Arrange the parts as desired, generally to minimize waste. Copy each body to be laser cut to a new component called ‘cut layout’ or similar.Arrange bodies into ‘components’ as appropriate. Model your project as for any other media.Taylor demonstrated it at one of his Fusion 360 workshops, and I’m sure more information can be found with a web search. It’s always been possible to use Fusion 360 to develop projects for our laser cutter. For non AMT readers, our laser cutter seems to be very similar to the RL-80-1290 sold by Rabbit Laser. These notes apply to our EXLAS 1280 laser cutter, which is driven by Lasercut 5.3 and accepts a DXF file as input. I recently experimented with this feature, and thought I’d write up my findings. Fusion 360 now has an experimental CAM feature to develop cutting paths for a laser cutter.
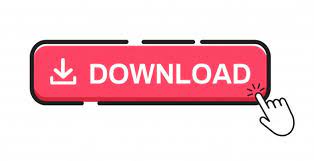